Fixed calipers can be made in one block (monobloc) or two separate pieces. Monobloc calipers, being made from a single casting, offer a better mass/fluid displacement ratio and shape flexibility due to the absence of screws or bolts. They also occupy less radial space as they have no conical draft.
On the other hand, two-piece calipers are easier to make and assemble because they do not require special tools to be machined.
The correct operation of brake callipers depends on a number of factors, including the quality of component workmanship, correct assembly and choice of materials. Piston smoothness, lining quality and volumetric absorption (meaning the volume of brake fluid that is absorbed during braking due to the deformation of the caliper) are other decisive factors for achieving fast and precise braking system response.
The main components of brake calipers
Brake calipers consist of several components:
Caliper body: It must withstand stress, ensure the pads are seated on the disc and accommodate the piston seats.
Cylinders: They house the piston and provide hydraulic sealing, allowing the piston to move smoothly while braking.
Pistons: They transform hydraulic pressure into mechanical force, applying it directly to the pads. They are made of thermally insulating materials to limit heat transmission from the pad to the brake fluid. They are also designed not to deform at high temperatures and to be compatible with brake fluid.
Sliding guides: They allow relative movement between the caliper body and the fixed support, ensuring that the braking force is applied evenly.
Seals: They ensure the sealing of the brake fluid and allow the piston to return to its original position after braking (roll-back function) despite being subjected to pressures of up to 350 bar and temperatures between -40° and +200° C. Similarly, but in the opposite direction, these special seals return the piston to its correct working position if the lateral deformation of the disc pushes it back (knock-back function). This ensures that the braking stroke is not longer than nominal. The piston seal must also be compatible with the fluid with which it will come into contact during operation (EPDM for DOT brake fluids, HNBR for mineral oils).
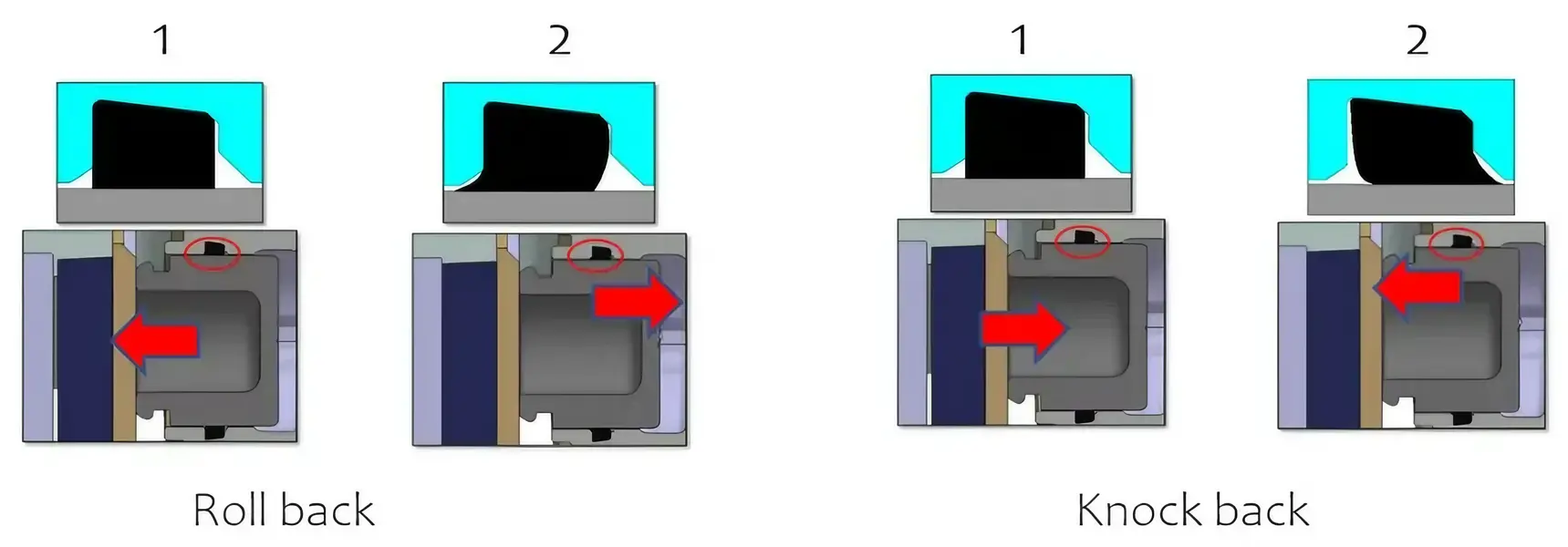
Dust covers: They protect the piston cylinder from dirt and moisture, preventing damage and corrosion.
Brake pad springs: They return the pads to their resting position after braking. The spring also keeps the pads adhered to their respective pistons. It is made of stainless steel or spring steel with an anti-corrosion coating.
Bleed screw: It allows bleeding by allowing air to escape from the caliper.
Fastening ears: These components fasten the brake caliper to the hub carrier. They can be radial or axial, depending on construction requirements.
Radial holes: They allow the use of larger diameter discs, limit deformation under torque and promote more even pad wear.
Axial holes: They are easier to drill because they are parallel, and also allow the mounting of floating calipers.
Lines
Other key components are the lines that feed the brake calipers. The lines can be flexible, made of rubber and metal braid and/or rigid metal pipes. The most suitable lines are chosen according to construction and performance requirements. For instance, brake lines on high-performance vehicles may consist of a rigid pipe segment near the caliper followed by a flexible hose. This solution is adopted because the rigid pipe provides adequate thermal insulation to protect the flexible part from the high temperatures coming from the caliper.
This article was modified from content published by Brembo. A link to the original article can be found here. To view our range of Brembo calipers, click here.